Electrical safety helmets are indispensable in industries where head protection combined with electrical insulation is necessary. These helmets not only shield workers from physical impacts but also prevent electrical current from reaching their heads, a crucial feature in sectors such as construction, electrical maintenance, and utility services.
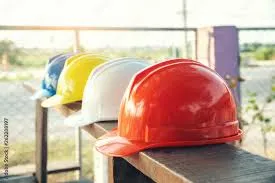
What sets electrical safety helmets apart from standard hard hats is their unique ability to mitigate the risk of electrical shock. Constructed with non-conductive materials, typically high-density polyethylene or fiberglass, these helmets provide a secondary layer of defense. The incorporation of a dielectric liner inside enhances their protective characteristics by offering higher resistance to electrical penetration. This dual-layer design ensures that even when the external surface of the helmet is in contact with a live electrical source, the wearer remains insulated.
For individuals working under high-voltage conditions, the choice of headgear can be a life-or-death decision. Certifications from authoritative organizations like the American National Standards Institute (ANSI) and the International Electrotechnical Commission (IEC) offer peace of mind, as they demand rigorous testing before endorsing a product. Helmets certified under standards such as ANSI Z89.1 or IEC 61240 have undergone tests for voltage withstand capabilities, impact resistance, and stability under both hot and cold conditions.
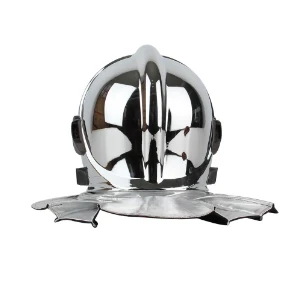
An expert assessment of electrical safety helmets underscores the importance of brand reputation and technological advancements. Market leaders consistently invest in research to enhance the durability and comfort of their helmets. Features like adjustable harnesses, sweatbands for comfort, and multi-environment adaptability are now standard in high-end models. Furthermore, the evolution of add-ons such as visor attachments and earmuffs, which do not compromise the helmet’s insulating properties, offer a comprehensive safety solution for workers.
electrical safety helmet
True expertise in selecting electrical safety headgear involves understanding the specific needs dictated by the working environment. Helmets designed for a controlled indoor facility might differ significantly from those intended for rugged outdoor settings, where exposure to elements like moisture and extreme temperatures could affect performance. Experienced professionals appreciate the nuances of helmet maintenance and inspection. Regular checks for cracks, material degradation, and proper fit are imperative to retain the helmet’s protective integrity.
Authoritative voices, including seasoned safety inspectors and industry veterans, emphasize ongoing education about electrical safety protocols. Training programs that include practical demonstrations of the protective capability of safety helmets foster a culture of safety and awareness. Trust is cultivated not just by the presence of safety equipment but through the demonstration of its effective use in real-world scenarios. Providing workers with knowledge and firsthand experiences about the protective measures available significantly reduces workplace accidents and elevates overall safety standards.
In conclusion, the world of electrical safety helmets is continuously evolving, with manufacturers pushing the envelope in terms of technology and user comfort. Professionals tasked with equipping their workforce should remain informed about the latest advancements and regulatory standards to ensure optimal protection. With the right choice of helmet, workers gain not only protection but also confidence to perform their duties in high-risk environments.